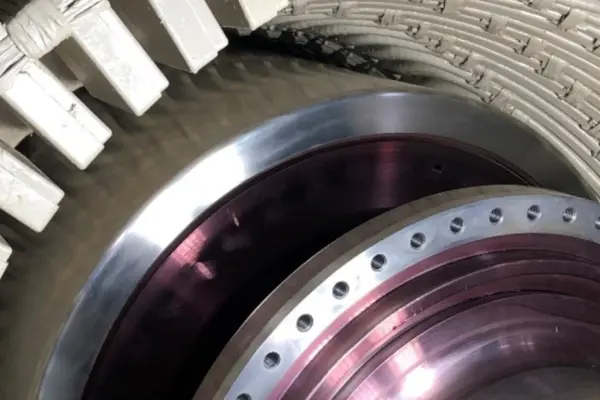
Using the latests robotics technologies to increase efficiency, prodcutivity and reliability
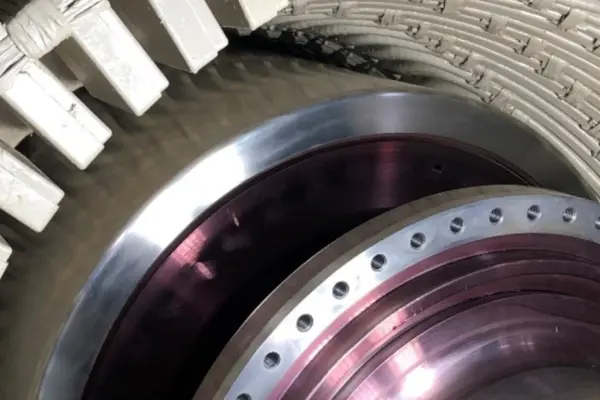
Using the latests robotics technologies to increase efficiency, prodcutivity and reliability
Electrical motor and generator inspection
Testing with rotor-in-situ technology
Turbo and Hydro generators as well as large motors are crucial components in an industrial power plant and are designed to operate reliably for many years. One of the most expensive parts of a 3-phase generator is the stator, which is where the energy from the magnetic field is converted into electrical energy/ mechanical energy. The condition of the stator core of a rotating electrical machine deteriorates over time, increasing the likelihood of failures. Quantitative testing and periodic inspections of the generator core are necessary to avoid outages.
- Condition of the Turbo generator/ Hydro Generator / Large motor
- Routine maintenance/overhaul
- Long-term condition
Measurements, inspections and testing
- Ohmic phase resistance.
- Polarization index and insulation resistance on each phase of the stator winding.
- Charge/discharge measurement of the stator winding.
- Overvoltage DC test, also referred to as high-potential or DC hi-pot tests.
- Tan Delta measurement on each phase and capacitance test.
- DC leakage test.
- Partial discharge measurements.
- Visual inspection of end-windings, winding connections, support system of end winding phase and series caps and ties.
- Visual inspection of terminal area: bushings, lower leads, stand-off insulators, connection to the bus ducts.