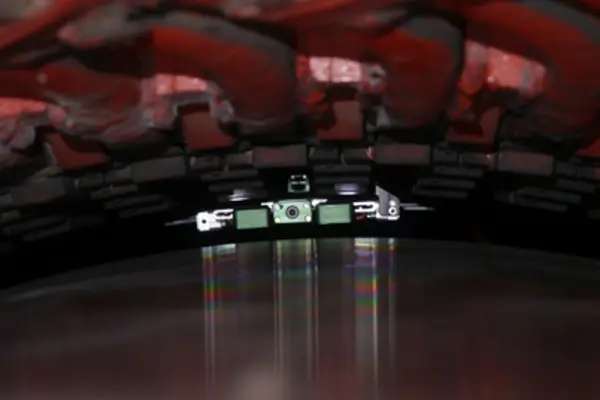
DEKRA Industrial Inspection
In-situ mechanical inspections without removal of the rotor
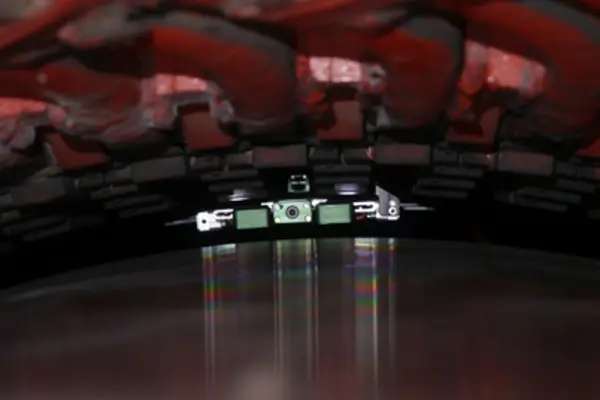
DEKRA Industrial Inspection
In-situ mechanical inspections without removal of the rotor
Advanced Robotic Generator Inspection System (ARGIS)
Major Savings for In Situ Inspection with ARGIS
ARGIS enables inspections to be carried out not only when the rotor has been removed, but also with the rotor still in place, thus saving you time, effort and money. Discover the possibilities here.
Condition testing normally requires the rotor to be removed from the generator. Not only could this possibly damage the generator, but it is also time-consuming work that can only be performed during a major shutdown. However, thanks to the Advanced Robotic Generator Inspection System (ARGIS) developed by DEKRA, removal of the rotor can be avoided. The ARGIS system is a proven concept for in-situ mechanical inspections which can be performed on many brands of generators.
How ARGIS works
A chain containing motor drives and a docking station for the Generator Inspection Vehicle (GIV) is mounted around one of the retaining rings of the generator. The chain is positioned accurately in front of each slot so that the GIV can be inserted into a gap as small as 17 mm (0,67 inch) and up. The GIV then moves to the other end of the stator core and back in order to perform the ELCID, wedge test and visual inspections all in the same run to save time.
The ARGIS air gap inspection can be performed in approximately 3.5 shifts, depending on the size and accessibility of the generator. If required, multiple teams can be sent to reduce inspection time. Removal of the shields, blades, coolers and electrical safety, approved scaffolding, illumination and cleaning is the responsibility of the client.
Electromagnetic core flux leakage testing (ELCID or equivalent) is a standard feature. The step irons are measured with a separate module. The low flux core test (equivalent to EL CID) on step irons is performed separately. Note: DEKRA is an independent company, not affiliated to any OEM or repair shop.
In which generators does the ARGIS robot fit?
The “air gap” is defined as the space between rotor and stator. However, the geometry of the retaining rings also determines whether the ARGIS robot will fit. The “entrance” gap is defined as the space between retaining ring and stator inner surface. The robot will fit if the entrance gap is 17 mm or larger. If the entrance gap is less than 17 mm, the ARGIS robot may fit, depending on the geometry of the step irons and the retaining rings.